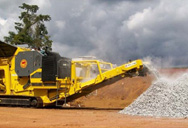
Vertical Roller Mills - FLSmidth
Stay updated on your industry Our highly-flexible vertical roller mills (VRM) are energy-saving grinding solutions that cater for differing types of material.
Charlar en Línea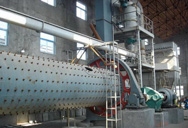
VERTICAL ROLLER MILLS A holistic VRM approach
The quadropol® vertical roller mill by thyssenkrupp Industrial Solutions takes a holistic approach to modern grinding systems in terms of its simple and compatible design.
Charlar en Línea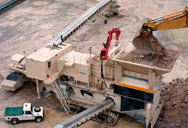
OK™ Raw and Cement Mill - FLSmidth
Our vertical roller mill offers optimum raw, cement and slag grinding Our best-in-class OK™ Mill is a globally successful vertical roller mill solution for grinding raw material,
Charlar en Línea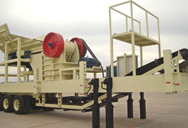
Optimization Design of the Lower Rocker Arm of a
2021.11.5 The lower rocker arm is an important part of the vertical roller mill and its lightweight design is of great significance for reducing the mass and production cost of the roller mill.
Charlar en Línea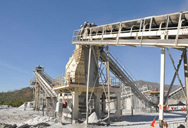
Operational parameters affecting the vertical roller mill
2017.4.1 The vertical roller mill (VRM) is commonly used for secondary and tertiary crushing processes in numerous industries. In this study, the discrete element method
Charlar en Línea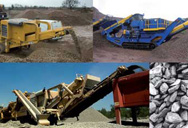
OK™ cement mill The most energy- efficient mill for cement
Proven commercially, the OK™ mill is the premier roller mill for finish grinding of Portland cement, slag and blended cements. The mill consistently uses five to ten percent less
Charlar en Línea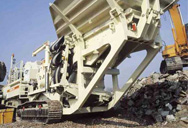
Grinding Technologies - thyssenkrupp Polysius
quadropol® vertical roller mill In the last years, thyssenkrupp has successfully continued stepwise the development process for the quadropol® vertical roller mill concept.
Charlar en Línea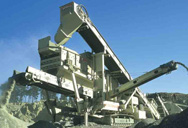
Atlas Vertical Roller Mill - NETZSCH Grinding Dispersing - PDF ...
The fundamental difference between the ATLAS and other table-roller mills is the bearing arrangement for the grinding table which is incorporated into the base of the mill. This
Charlar en Línea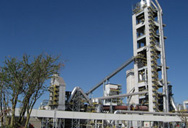
Optimization Design of the Lower Rocker Arm of a Vertical Roller Mill ...
2021.11.5 design is of great significance for reducing the mass and production cost of the roller mill. Firstly, the strength and deformation distribution of the lower rocker arm under working load were analyzed by ANSYS Workbench to determine the maximum stress and maximum deformation. The parts with large strength margin were used as the basis
Charlar en Línea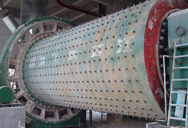
Vertical roller mill for raw Application p rocess materials
Vertical roller mills are adopted in 20 cement plants (44 mills) in Japan. Results Table Energy saving effect of the vertical roller mill Ball mill Specific power Cost estimation About 14million US$ [Newly-built] and about 230 million US$ [retrofitted], including the cost of supplemental facilities [200t-RM/h] [1US$=¥110] Related matters ...
Charlar en Línea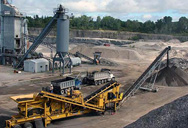
(PDF) Performance Evaluation of Vertical Roller Mill
2017.9.11 Due to the compact design and material transportation system of vertical roller mills (VRM), some important streams (total mill feed and discharge, dynamic separator feed and reject) remain in the ...
Charlar en Línea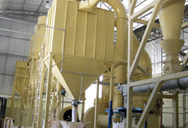
A study of operating parameters of a roller mill with a new design ...
2019.2.21 The influence of modifying the working unit by inserting a vertical plate between cooperating rollers on performance indicators – fineness, energy ... among other things, on friction conditions, collision, cutting, new mill design features. The new design of roller mill assembly consists of two rotating rollers with ...
Charlar en Línea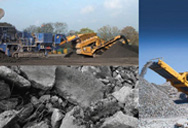
MPS vertical roller mill - Gebr. Pfeiffer
The MPS vertical roller mill - built to last, reliable and energy-efficient - is the optimum solution when it comes to performing several process steps in one unit. Advantages of the MPS vertical mill . Low capital expenditure . ... Design measures preventing pulverized coal deposits: 6: Rollers can be lifted off: 7: Pull rods outside mill housing:
Charlar en Línea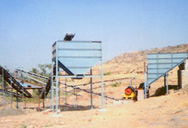
Optimization Design of the Lower Rocker Arm of a Vertical Roller Mill ...
2021.11.5 The lower rocker arm is an important part of the vertical roller mill and its lightweight design is of great significance for reducing the mass and production cost of the roller mill. Firstly, the strength and deformation distribution of the lower rocker arm under working load were analyzed by ANSYS Workbench to determine the maximum stress
Charlar en Línea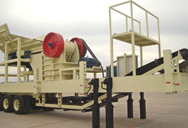
MAAG® GEAR CEM Drive - FLSmidth
Our best-in-class OK™ Mill is a globally successful vertical roller mill solution for grinding raw material, cement and slag. Its cutting-edge design features consistently deliver the highest quality products with the greatest efficiency. It is affordable to install and cost effective to operate over your cement plant’s lifetime.
Charlar en Línea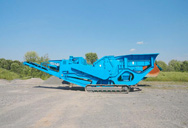
VRM – AMCL Machinery Limited
UBE Vertical Roller Mill performs drying, grinding, ... UBE’s mill design and rich experience of more than 260 Mill installation allows us to handle coal which is combustible and volatile in nature by ensuring safety and efficient grinding efficiency.
Charlar en Línea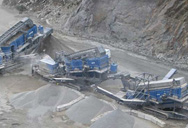
On the Optimization Procedure of Rolling Mill Design
2012.9.27 It is a combination of software and hardware design concept. Eight optimization steps – pass schedule generation, work roll determination, backup roll diameter, mill type selection, mill window ...
Charlar en Línea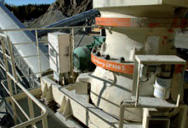
Operational parameters affecting the vertical roller mill
2017.4.1 In the air-swept mode, the vertical-roller-mill and a high efficiency dynamic classifier are suited above each other as a single unit (Fig. 1). ... The design and manufacture of large vertical roller mills. Zement Kalk Gips, No.2 (1993), pp. 40-43. View in Scopus Google Scholar.
Charlar en Línea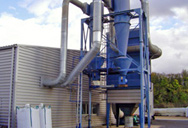
Operational parameters affecting the vertical roller mill
2017.4.1 A cement Vertical Roller Mill modeling based on the number of breakages. Vertical roller mills (VRM) are widely used to grind, dry, and select powders from various materials in the cement, electric power, metallurgical, chemical, and nonmetallic ore industries. For the sectors above, the VRM is a powerful and energy-intensive grinding
Charlar en Línea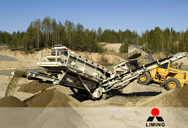
Selected Aspects of Modelling and Design Calculations of Roller
2021.3.1 values of κ = 8080.64 N for the roller made of steel and for κ = 7720.96 N for the roller made. of cast iron were received for the roller’s angular speed ω1 = 1.6 rads. In Figure 5, the ...
Charlar en Línea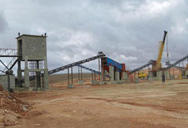
DRIVE SELECTION FOR LARGE LOESCHE VERTICAL ROLLER MILLS
tem for a new, high-capacity vertical roller mill, and explains the thinking behind the decisions made. After a summary of the most important functions of the drive for a vertical roller mill, its design and design limitations, there is a detailed comparison, using a real project, to select the best available drive system.3
Charlar en Línea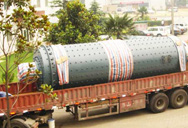
VERTICAL ROLLER MILLS A holistic VRM approach
VERTICAL ROLLER MILLS 1 SEPTEMBER 2021 INTERNATIONAL CEMENT REVIEW P ut simply and briefly, thyssenkrupp’s quadropol® vertical roller mill (VRM) remains one of the leading VRMs in the market in terms of its simple and compatible design structure. Requirements by plant operators for a reliable solution, as well as not requiring tie rods to ...
Charlar en Línea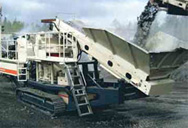
Vertical roller mill - Welding Alloys
During the height of the COVID-19 pandemic, Welding Alloys undertook a project to repair a vertical roller mill (VRM) at Hanson Cement’s site in Purfleet, Essex. The work involved the repair of a Loesche 46 2+2S VRM grinding table and rollers, which suffered extensive wear during the processing of 3 500 tonnes of granulated blast furnace slag.
Charlar en Línea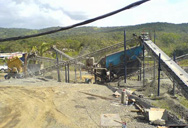
PROCESS CONTROL FOR CEMENT GRINDING IN VERTICAL ROLLER MILL
Keywords: vertical roller mill, model predictive control, proportional integral and derivative control, artificial neural networks, fuzzy logic. 1. INTRODUCTION The VRM is a type of grinding mill integrated with multi functions such as grinding, drying and separation, used for grinding of coal, petroleum coke and minerals.
Charlar en Línea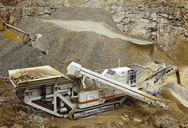
Cement grinding Vertical roller mills VS ball mills
For a ball mill grinding OPC to a fineness of 3200 to 3600 cm2/g (Blaine) the cost of wear parts (ball, liners and mill internals) is typically 0.15-0.20 EUR per ton of cement. For an OK mill grinding a similar product, the cost of wear parts depends on the maintenance procedures, i.e. whether hardfacing is applied.
Charlar en Línea
Strength Assessment of Heavy Load Cast Iron Machine Part
2021.6.8 by Korte, W.; Klokow, A.; Bettenworth, J. This paper presents how Loesche evaluates the rocker arm of a vertical roller mill with the help of S-Life FKM by PART Engineering with respect to static strength and fatigue strength according to the FKM guideline [1]. For this purpose, first the functioning of the vertical roller mill and in detail
Charlar en Línea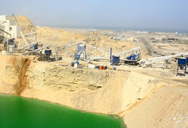
Grinding Technologies - thyssenkrupp Polysius
In the last years, thyssenkrupp has successfully continued stepwise the development process for the quadropol® vertical roller mill concept. This compact and modular conception includes the latest market requirements regarding compact plant layout, efficient operational process, reliable machine design and reduced unscheduled down time.
Charlar en Línea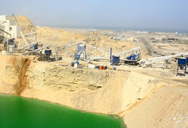
Optimization Design of the Lower Rocker Arm of a Vertical Roller Mill ...
2021.11.5 Abstract and Figures. The lower rocker arm is an important part of the vertical roller mill and its lightweight design is of great significance for reducing the mass and production cost of the ...
Charlar en Línea